Al hablar de emprendimiento, siempre nos centramos en los fundadores, los CEOs y demás. Pero esta no es una de esas historias. Cuando preguntamos a nuestro protagonista, Antonio Alarcón, qué cargo tiene para incluirlo en este reportaje, responde entre risas: “No tengo ninguno. Llámame trabajador, ¡qué mejor piropo que ese!”.
Su vida podría haber sido muy diferente. Hoy podría seguir al volante de un camión o de un autobús, que fue lo que hizo siempre, hasta que un glaucoma lo dejó con un diez por ciento de visión. Otro se lamentaría. Él es el buen humor personificado. Se ríe por cualquier motivo y, lo que es más importante, gracias a él muchas otras personas con problemas de visión pueden tener una vida más independiente y más segura.
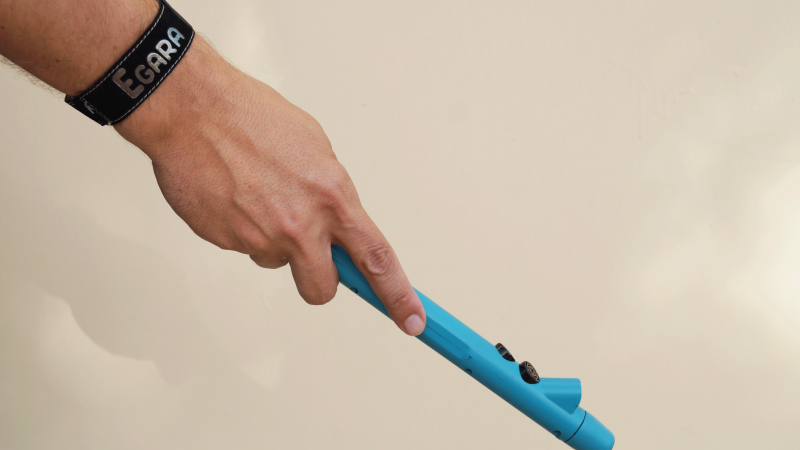
Egara se adapta a cualquier bastón de aluminio. Imagen: Instead-Technologies
Toda mi vida he trabajado y con treinta y pico años me detectaron el glaucoma ya muy avanzado. El trauma fue bestial
Camino difícil
El camino no ha sido fácil. "Toda mi vida he trabajado y con treinta y pico años me detectaron el glaucoma ya muy avanzado. Imagínate el golpe cuando te dicen que eres ciego y el día antes pensabas que veías perfectamente. El trauma fue bestial. Tuve una depresión, lo pasé muy mal. Me jubilaron y a partir de ahí mi vida fue aburrimiento puro y duro”, relata.
Por suerte -según sus propias palabras- conoció al equipo de Instead Technologies, que fabrica dispositivos a medida y sobre todo robots para rehabilitación tras un ictus: “Me dijeron que fuera a las oficinas, aunque fuese a coger el teléfono. Me daban cosas que hacer. No sé por qué vieron que era una persona válida, ellos sabrán, ríe”.
Le pregunté al técnico cómo protegerme cuando me encontrase con algo que me diera en la cabeza. Me dijo que no hay ninguna técnica
Adaptación
En el proceso de adaptación a su nueva situación, salió a la calle con un experto de la ONCE para aprender a manejar el bastón. “Estuve a punto de golpearme con una escalera. Le pregunté al técnico qué pasaba cuando me encontrase con un toldo o algo que me diera en la cabeza, cómo podía protegerme. Me dijo que no hay ninguna técnica, que si quería podía salir a la calle con la mano delante de la cara”, explica.
De vuelta a la empresa, a sus compañeros les resultó extraño que no existiese una solución para ese problema. “Empezamos a darle vueltas y a estudiar. Se habían hecho muchas cosas, pero nunca habían tenido éxito porque eran muy complejas o porque detectaban los obstáculos a los lados y te daban una información que no necesitabas”, recuerda.
Queríamos desarrollar un sistema que se adaptara al usuario
Solución
Al final, tomaron la decisión de desarrollar “un sistema que se adaptara al usuario”. Todo, con su propios medios, pagando los prototipos, “porque somos una empresa muy pequeña”.
Ahora, Egara es una realidad. “Fabricamos un mango que se puede adaptar a los segmentos de aluminio de cualquier otro bastón que ya haya en el mercado” -explica- “que detecta los obstáculos que hay desde la cintura hasta la cabeza. Pero solo los que podrían golpear al usuario, no los que quedan a un lado. Por tanto, los avisos deberían ser mínimos”.
Cuando hay un obstáculo que puede golpear a la persona y que no es detectable por el puntero del bastón -como una rama de árbol, un espejo retrovisor de un camión o, en el caso de Antonio, un toldo- el mango hace vibrar la pulsera que lleva conectada. El sistema cuenta con tres sensores de ultrasonidos, una placa electrónica “que hemos creado nosotros” -resalta- y un giróscopo de seis ejes que determina la posición del bastón en cada momento del barrido y lanza los ultrasonidos solo cuando pasa frente al usuario. “De esa forma, no es la persona quien adapta sus movimientos, sino que es el propio bastón el que se adapta a los del usuario, haga el barrido más amplio o más estrecho”. Además, también tiene en cuenta la estatura de la persona usuaria.
Eso ha sido, según sus palabras, lo más difícil: “Que sea sencillo, natural y que una persona pueda utilizarlo en cuestión de dos minutos.
Ahora llega el reto de hacerlo viable desde un punto de vista empresarial
Viabilidad
Ahora llega el reto de hacerlo viable desde un punto de vista empresarial. “El gran problema que tenemos es que fabricarlos a pequeña escala supone que al ponerlos a la venta el precio suba a 400 o 500 euros y la gente no está ahora en disposición de gastarse ese dinero”, razona.
Por eso, ser el proyecto ganador en los Premios a la Innovación Social de la Fundación MAPFRE en Europa en la categoría Movilidad sostenible y seguridad vial , no ha sido suficiente. “Queríamos ganar el premio a nivel mundial, porque con esos 30.000 euros podíamos comprar moldes de plástico de inyección para fabricar las piezas, que es lo más caro. Con eso habríamos reducido casi 200 euros cada unidad”. Ahora las imprimen en 3D.
Aun así, Antonio asegura que no se van a rendir: “Nuestro objetivo es encontrar la fórmula para que a la gente no le suponga un coste mayor de 250 euros”. Y añade rotundo: “Estamos emperrados en sacarlo a la calle y luego que la gente decida si es útil o no”.